Collapsible Core Injection Molding Service
In the past 20 years, the company has focused on and perfected the Collapsible core injection molding process, paying attention to every detail with the highest quality and requirements, using modern equipment to focus on the latest Collapsible core injection molding lean manufacturing process, saving you more time and money. This means that we can keep your products at a competitive price to win more customers and markets. In order to start your next foldable core project, we promise that any inquiries will receive prompt attention.

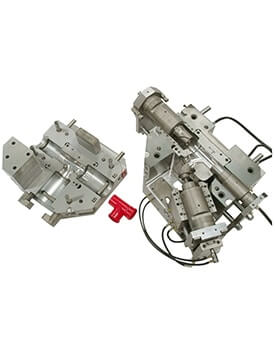
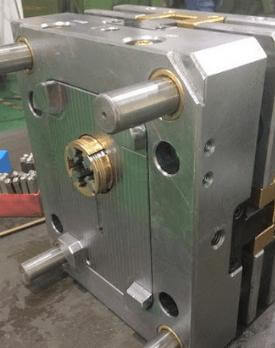
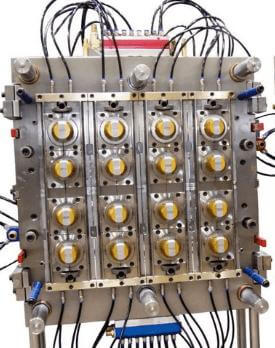
Collapsible Core Injection Molding Parts
With our state-of-the-art precision equipment, Dongqing manufactures foldable core molds and products for all applications, providing high-quality products at competitive prices. We manufacture Collapsible core molds for a wide range of industries.
China Collapsible Core Injection Molding Manufacturer FAQ
Collapsible Core Injection Molding Service – Ultimate FAQ Guide
Collapsible mold cores are usually used for product buckling, threading, etc. demoulding. It is a new type of mold structure that has the advantages of simple structure, less mold space than traditional molding structures, and cost savings. We know how to produce high-quality Collapsible core molds quickly and efficiently, and deliver your molds in time.
As a professional manufacturer of foldable core material injection molding, we have 24 years of experience. Holly has paid 100% enthusiasm for you. Here is a list of frequently asked questions about Collapsible core injection molding.
[lwptoc skipHeadingLevel=”h1″ skipHeadingText=”*Collapsible Core Injection Molding Service|*Collapsible Core Injection Molding Parts|*Factory|*Client Visiting|*China Collapsible Core Injection Molding Manufacturer FAQ|*What is a Collapsible core?|*How to check the completion of the Collapsible core?|*What are the advantages of Collapsible core injection molding?|*What are the core features of Collapsible ?|*What CAD type do you accept?|*How to get a quotation for the mold cost and part price?|*Are You Looking For Collapsible Core Injection Molding Manufacturer?|*Get a quick quote|*Collapsible Core Injection Molding Service – Ultimate FAQ Guide|*Send Your Inquiry Now”]
Collapsible mold cores are usually used for product buckling, threading, demoulding. It is a new type of mold structure that has the advantages of simple structure, less mold space than traditional molding structures, and cost savings. We know how to produce high-quality Collapsible core molds quickly and efficiently, and deliver your molds in time. As a professional manufacturer of collapsible core material injection molding, we have 24 years of experience. Holly has paid 100% enthusiasm for you.
Here is a list of frequently asked questions about Collapsible core injection molding.
1. What can Holly do if customers need Collapsible core injection molding?
Holly can tailor origami mandrels according to your needs, be cost-effective, and help you win more markets. We strive to develop a strong and lasting business relationship with you.
From part design, mold design, mold making, mold trial production to production, we provide in-house die and mold processing, concave injection molding, collapsible core injection molding, collapsible core mechanism design, manufacturing. The core customization of the dovetail collapsible and the foldability of the core tool construction. In addition, the Holly team will provide customers with high-quality services.
When customers need our help, we can solve the problem on the spot. We provide customers with professional Collapsible core injection molding technology.
2. Why choose Holly as the manufacturer of Collapsible core injection molds?
Since Holly has focused and perfected the Collapsible core injection molding process over the past 20 years, she has utilized modern equipment to follow the latest Collapsible core injection lean manufacturing process, saving her customers money and time. This means that we can keep your products at a competitive price to win more customers and markets.
If you want to start the next collapsible core project, Holly promises that any inquiries will receive prompt attention. The Holly team will do our best to support you and welcome you to send us a video call when necessary.
3. What is a collapsible core?
Collapsible mold core release technology is one of the key technologies in mold injection. Suitable for parts whose inner cavity size is larger than the outer cavity size, The demoulding was rapid during injection and the demoulding was successful.
Collapsible cores are usually used in the following industries: automotive industry, electrical engineering, food industry, medical technology, furniture industry, sanitary engineering, toy industry, process measurement and control technology, packaging industry.
Collapsible core injection molding can reduce the processing cost by more than 12%, shorten the processing cycle, and increase the output. Therefore, collapsible core injection molding is widely used in the production of cosmetic bottle caps, water pipes, and daily necessities bottle caps.
4. What are the advantages of Collapsible core injection molding?
The advantages of Collapsible core injection molding are as follows:
- It not only reduces the number of cycles and maintenance but also saves costs.
- Collapsible core injection molding can reduce processing costs by more than 12%,
- Shorten the processing cycle.
- Collapsible core injection molding is widely used in the automotive industry, electrical engineering, food industry, medical technology, furniture industry, sanitary engineering, the toy industry and so on.
- Collapsible core injection molding is especially suitable for producing composite plastic products with complex shapes, hollow, and not suitable for mechanical processing.
- Accurate internal dimensions and clean surface hollow plastic products are only possible with Collapsible core injection molding.
5. What are the core features of collapsible?
The core features of collapsible are as follows.
- 1) Ingenious structure, moving and demoulding in limited space.
- 2) High precision and consistency of parts.
- 3) Cold processing technology for high hardness materials.
- 4) Safe and reliable mechanical structure of multi-cavity injection mould makes the mould size smaller.
6. What is the composition of the collapsible core?
The collapsible magnetic core is composed of three parts, with simple installation, reliable operation and long service life. The three units are a collapsible core, a centre pin, and a front Collapsible sleeve.
- The core of the centre
- 6 external segments
- Moving ring
- 2 half-ring
- Cooling hole
- O-ring seal groove
- Lock pin
7. What is the purpose of the centre pin in the Collapsible core?
The centre pin serves to expand the position of the collapsible core-forming part and keeps them at this diameter.
8. What is the ideal operating sequence for the automatic operation of the Collapsible mold core?
The molding sequence can easily follow the start and open presses:
The press opens and the mold parts are on the main parting line. A mechanical or hydraulic knocking media moves the ejector plate assembly forward when the mold is fully opened. The top firing plate assembly and the collapsed core are the stroke required to move forward, to move the core away from the center pin and collapse the core (this is the first stage of ejection).
At this stage, if the core section fails to collapse for any reason, the positive collapse sleeve will play a role to ensure the beginning of the collapse. In addition, since the return pin is located directly below the discharge plate, the discharge plate and the ejector plate assembly move together. This simultaneous movement continues until the ejection plate assembly is fully forward. At this time, a limit switch is activated. In this way, in turn, drive the cylinder to take over, and continue to move the stripper and insert the stripper, move the parts Stay away from the collapsed core (second stage).
9. Which stage is used to determine whether a part can be formed on the collapsible core?
- Weaken
- Loss of crash
- Shrink
- Clearance
10. What is the collapsible core mold design checklist?
- Use a guide ejector plate and a support ring around the center pin. The thimble plate, support ring and rest button must be polished to 1.187001.
- Use a spring to ensure the first break of the main parting line.
- Return the pin to the bottom of the discharge plate.
- The ejection board runs to specification. Print the size on the edge of the printing plate.
- The drive of the secondary stripper only starts after the full ejection stroke. Before the ejection plate begins to return, the stripper plate must be fully returned.
- Good ventilation is essential, preferably outside the mold.
- The gap between the core closing outer diameter and the inserting inner diameter of the stripper is. 0010/. 0015 total. Measure after inserting the core into the mold. Cone closure is not allowed. Avoid too long closing length; .150 /. 250 years is enough.
- The installed core can rotate freely when the board assembly is ejected.
- The centre pin is concentric with the stripping bushing. Verify that the protruding pin passes through the core and the radius is at the tip of the pin.
- Fold the sleeve actively to travel freely through the sheet. Apply grease to the indicated area. Check whether the mold moves freely at working temperature.
- When the face of the collapsible core part is closed to the cavity (some parts have through holes), all cores must be ground to the same O.A.L. The normal tolerance of 0.003 is not enough. Refer to Core Grinding Instructions. The gap between the end of the core surface and the cavity is .0005 to .00.
- Don’t preload the core. When the above situation occurs, the early ejector plate must be used to return to the system, otherwise, the core will be destroyed.
- Note: This only applies to the core seal cavity. When the pin rests on the cavity, care should be taken to avoid excessive preload of the pin. A disturbance of 0.00000 to 0.0015 is sufficient.
- Break all sharp corners.
- The diameter of the closing tube of the stripper must be the same as the other diameters on the core, or preferably larger than any other diameter.
11. What type of collapsible core?
The types of collapsible cores are as follows:
1) Dovetail collapsible core
The aggressive, mechanically driven Collapsible core eliminates complex gear and rack methods, resulting in simpler molds and faster cycle times.
2) RT collapsible core
Parts with internal protrusions, dents, interrupted threads and cuts can now be produced economically on a high or low volume basis.
3) Extensible tooth decay
Develop mold parts and external details such as threads, ribs, grooves, barbs, and dimples without the need for traditional side action components.
12. When a customer needs a collapsible core, what kind of engineering services will Holly provide?
1) Design review of molded products.
2) Mould design review.
3) Shaping the product design. (DFM)
4) Complete or partial mold design.
5) Virtual and on-site maintenance training.
6) Mold modification design. (Unscrew the collapsible core)
7) Regardless of your engineering requirements from the simple mold part 8) Change suggestions to complete the mold design, the Holly tool engineering team is here 9) Support you in all ways to bring success and beneficial experience to you and your customers.
13. What industries are Collapsible cores usually used for?
- Automotive industry
- Electrical engineering
- Food industry
- Medical technology
- Furniture industry
- Sanitary Engineering
- Toy industry
- Process measurement and control technology
- Packaging industry
14. What can Holly do when customers need a collapsible core?
You can rely on our comprehensive and comprehensive support.
- We will tell you in detail how to use your collapsible core.
- We design your collapsible core in 2D and 3D. You will get the data of the collapsible core for further tool design.
- We produce your collapsible core and its complete profile.
- According to the plastic used and the temperature of the tool, we wrap your collapsible core.
- When you order a collapsible multi-cavity mold core, you can enjoy a price discount.
- Your collapsible core can be reprocessed, modified, adjusted, and even repaired. For example, have you noticed that after sampling, the plastic shrinks in a different way than expected, and we can adjust your collapsible core after inspection. The thread can also be grounded again.
15. What are the characteristics of the collapsible core?
The features of the collapsible magnetic core are as follows:
Collapsible cores are designed and manufactured according to customer specifications, so they can be manufactured to meet any requirements. This will make it possible to produce various contours with diameters ranging from 8 mm to 240 mm and contour lengths up to 130 mm. The total length of the collapsible core will be determined separately.
16. Why are Collapsible cores so important to reduce costs?
Collapsible core is an ideal solution for removing injection molded parts with folded edges or claws or threaded parts that are removed from the mold in a cost-effective manner. 12% of the hemming can be removed without any problem, and even 17% can be removed under special circumstances.
17. Why choose a Collapsible core?
1) Zydron core Zydron core adopts the latest wire technology.
2) This process allows our parts to maintain tighter tolerances, giving you a longer life and less production slowdown.
3) Direct sales increase the contact surface between the center pin and the Collapsible core, improve heat transfer, shorten cycle time, and reduce production costs.
4) Our flush core product has a needle and does not need to protrude past sleeves. This allows the product design to be maintained without being changed. This actually reduces the volume of each part where the plastic is molded and has a thin top surface part, reducing material costs.
18. What are the characteristics of the Collapsible mandrel?
Easily demoulded/ejected parts, with recesses, protrusions, or cuts can be cored injection moulds
19. What is needed to check the finish of the Collapsible iron core?
- Surface finish
- Due to improper grinding, there are concave edges and back hooks in the direction of collapse
- Comply with appropriate design procedures.
20. What are the core features of collapsible?
- Ingenious structure, moving and demoulding in limited space.
- High precision and consistency of parts.
- Cold working technology of high hardness materials.
- The safe and reliable multi-cavity injection mould mechanical structure makes the mould size smaller.